IARC
THE INTERNATIONAL AERIAL ROBOTICS COMPETITION
The International Aerial Competition (IARC) is the world's longest-running collegiate aerial robotics challenge, whose primary goal is to “move the state-of-the-art in aerial robotics forward.” To succeed with this ambitious goal, IARC poses challenges deemed “impossible” when introduced. The missions remain the same until one or more teams complete the challenges. The first IARC was held in 1991, and the longest-running mission, Mission 6, persisted for 8 years before the Georgia Institute of Technology solved the task. In 2023, Ascend was announced as the winner of Mission 9, four years after its introduction.
IARC MISSION 10
One year after Ascend wining mission 9, mission 10 was finaly released, addressing the pressing threat of anti-personnel mines—explosive devices designed to detonate upon contact, endangering soldiers, civilians, and children alike. The mission aims to empower a person-at-risk to cross a 100-meter minefield in under 10 minutes. Utilizing a swarm of four lightweight autonomous drones, the individual navigates this perilous terrain as the drones scout ahead, identify mines, and visually guide safe passage while creating a real-time digital map accessible via mobile phone. Focusing on coordination, mapping, and communication, Mission 10 emphasizes speed and situational awareness to ensure the person-at-risk successfully crosses the minefield before time runs out.
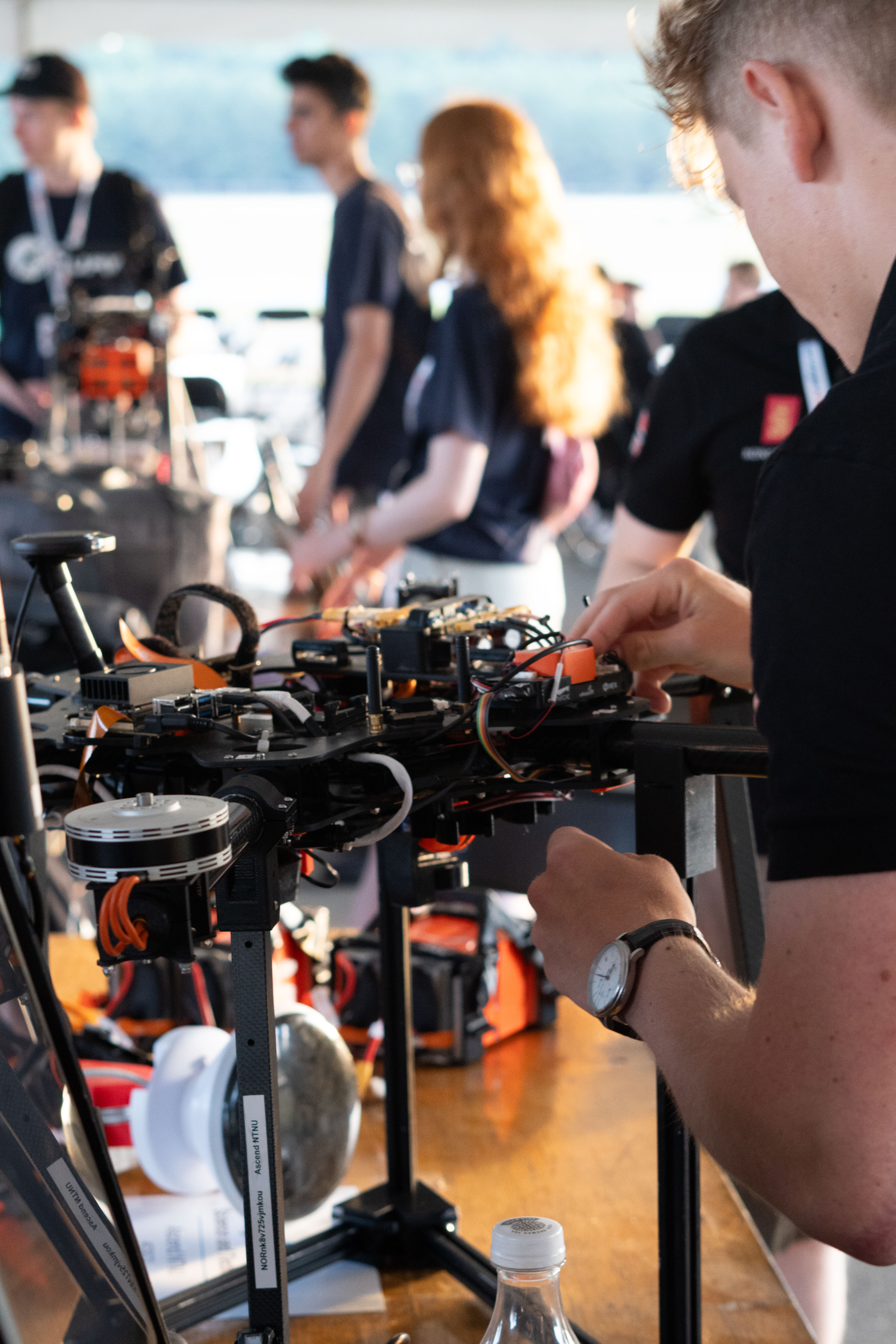