MARLIN
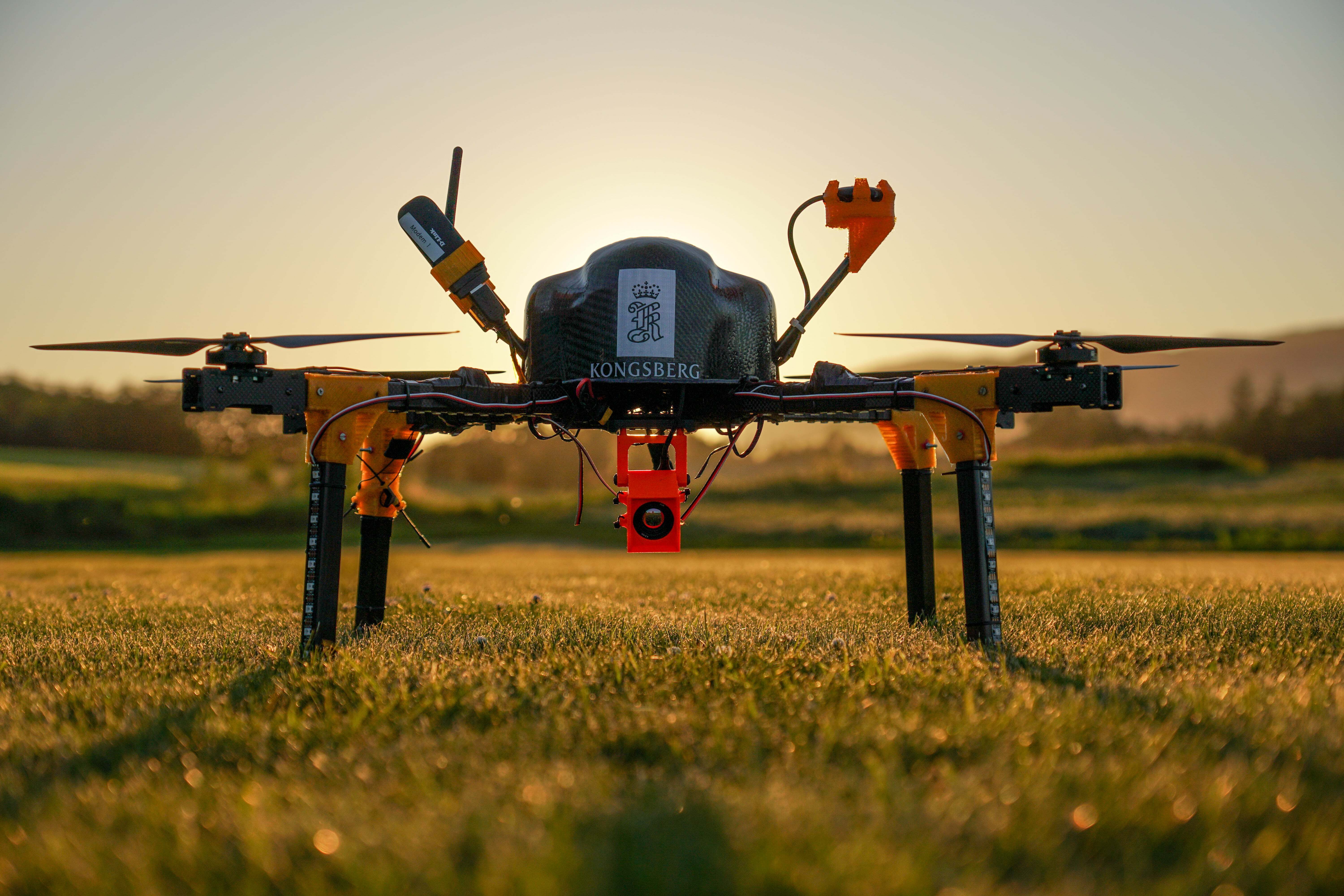
Marlin is our first outdoor drone designed for remote operations for TAC challenges.
Adapting to TAC mission scenarios, Marlin is our first drone to open up a new software pipeline in autonomous operations: AI decision-making and autopilot. The built-in AI system utilizes a “Superfluid” state machine and MAVROS package to enable extended flight beyond visual line of sight (BVLOS). Marlin employs thermal imagining to detect heat signatures from human-like objects for search and rescue scenarios. Other key characteristics include a powerline avoidance system and a failsafe mechanism.
The main frame is equipped with a custom antenna and various sensors for a gimbal, RGB thermal camera, Real Time Kinematic (RTK), and Pixhawk-based flight controller. The key takeaway from the name Marlin is its survivability under harsh weather conditions. This means that external hardware is made of waterproofing materials. In addition, Marlin is a lightweight A3 drone weighing only 2.4 kg with all essential accessories. Adapting to TAC mission scenarios, the drone can carry out regular flights with an additional 2.2 kg weight.
After winning first prize at the 2021 TAC challenge, Marlin is now retired as an outdoor test drone.
NOSTROMO
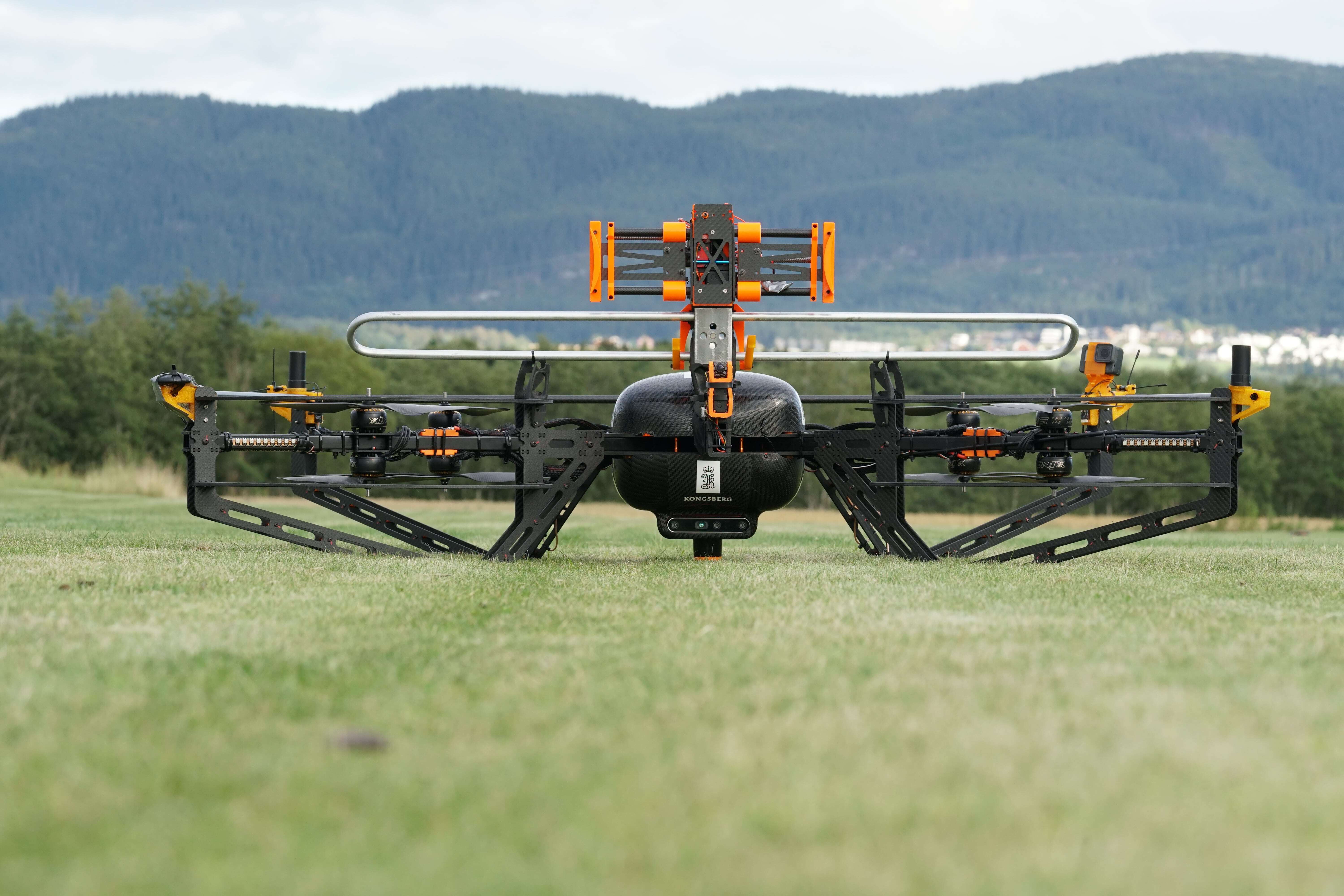
Nostromo is Ascend’s longest-established drone for IARC Mission 9 from 2020 to 2022. In 2020, the development was extended for a year due to COVID restrictions. This granted us time for massive upgrades from the original prototype.
Hardware accessibility is comparably faster and easier. In 2021, the drone’s mainframe design embraced a two-layered structure with additional mounting holes and frame capacity. The triangular-shaped legs have multiple contact points to the front and back arms. The extra frame space improves customizability without redesigning the entire frame. Meanwhile, the curved legs make the drone rigid and resistant to impacts and pressure.
The software system incorporates conventional deep-learning algorithms for recognizing edges, shapes, etc. Many simplifications were made using OpenCV as one of our main software frameworks. For example, 3D data processing was done through an off-the-shelf depth camera from Intel. The built-in software solutions fully convert software commands through GPS and orientation data, which is the foundation of Nostromo’s behavior.